半導體封裝、測試用的治具,如何使用精密雷射與蝕刻來製作?
半導體治具製造技術是現代科技的核心,它推動了電子產品、通訊設備、自動化技術的飛速發展。在半導體製造過程中,封裝與測試是關鍵步驟,而這些步驟需要高度精密的治具來確保操作的準確性。治具是用來固定、校準或測試半導體元件的專用工具,其設計與製作需達到極高的精度,才能滿足半導體製造中嚴苛的要求。
隨著技術的進步,傳統的加工技術已經無法滿足現代半導體行業對於治具精度和效能的需求。為了解決這一挑戰,精密雷射與精密蝕刻技術的結合成為製作高精度治具的主要技術手段。本文將深入探討如何使用這兩項技術來製作半導體封裝和測試用的治具。
半導體精密雷射切割治具
T=1.0mm 153x260mm
精密雷射技術的介紹與應用
在治具設計與製造中,精密雷射加工技術具有無可替代的優勢。雷射切割能夠精確地處理金屬與非金屬材料,使其達到微米級別的精度。這對於製作複雜形狀及細節要求極高的治具至關重要。尤其是在半導體封裝測試中,需要治具具備高度的一致性與穩定性,雷射技術能確保每個工件都符合嚴苛的尺寸與形狀要求。
精密雷射切割的優點不僅在於精度高,還在於它的速度快且適應性強。透過電腦數控系統,雷射機器能夠快速地在不同材料上執行高精度的切割,從而大幅縮短製造時間。此外,雷射技術還可以在不改變材料本身性質的前提下進行非接觸加工,配合高品質材料的使用,減少傳統機械加工所造成的材料變形或損耗。這在製作薄型、輕量的治具時尤為重要。
1. 雷射切割
雷射技術最常用於半導體治具的初步切割階段。通常,半導體治具使用不鏽鋼、銅等材料製作,而雷射切割能夠精確地按照設計圖紙切割這些材料,形成所需的外形。這種高精度的雷射切割技術,確保每個元件都能準確無誤地固定在治具上。
2. 雷射打孔
與微細加工在半導體封裝與測試過程中,治具常需要開設微孔以進行定位或放置測試探針。雷射技術在這方面具有絕對優勢。透過高能光束,雷射能夠以極高的精度在金屬或其他材料上打出直徑非常小的孔,並保持孔壁光滑以及較少的毛刺或毛邊,這對測試的準確性至關重要。
3. 非接觸加工
雷射技術屬於非接觸式加工技術,信昌公司經過特別設計的雷射切割機器,可以降低對材料施加物理壓力或熱量,尤其配合高品質材料的使用更可以大幅減少引發材料的變形或損傷。因此可以避免材料的變形、裂紋等問題,特別是在處理高精度的微小結構時,這一點尤為關鍵。

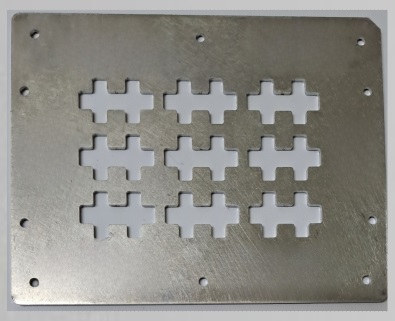
半導體封裝雷射切割治具
T=1.2
蝕刻技術應用與介紹
蝕刻技術是另一種高精度加工方法,常用於製作微小結構或圖案。蝕刻可以通過化學反應(濕式蝕刻)或物理反應(乾式蝕刻)去除材料表面,形成所需的形狀或結構。在半導體治具的製作中,蝕刻技術被廣泛應用於微細結構的加工,如細小的通孔、溝槽、或表面圖案等。
1. 濕式蝕刻
濕式蝕刻是一種化學蝕刻技術,通過化學溶液來溶解材料表面不需要的部分。這種技術適合大面積、均勻的材料去除,特別是在需要製作精細圖案或多層結構的治具時,濕式蝕刻能提供極高的精度。
2. 乾式蝕刻
乾式蝕刻主要使用等離子體技術來去除材料表面,通常用於製作更精細的結構。乾式蝕刻的優勢在於其對材料具有高度的方向性,可以控制蝕刻的深度與寬度,這使得其在製作微小的三維結構時非常有效。
3. 蝕刻技術的應用
蝕刻技術常被用於處理那些雷射技術難以實現的精細細節。例如,在治具上製作微孔或精細的表面圖案時,蝕刻技術能夠保持高度一致性並且不會損害材料的整體性。這對於測試治具中用於測試探針插入的細小孔洞,或者表面需要精細導流結構的部分非常實用。
精密雷射與蝕刻技術的結合
精密雷射加工與蝕刻的結合,提供了更靈活且高效的治具製作方案。在許多半導體封裝與測試治具的製作中,會使用雷射技術進行大致形狀的切割,搭配使用蝕刻技術來細化特定區域,最終達到精確且符合需求的精密測試治具設計。這種結合加工方式不僅提高了生產效率,還能保證治具的高精度和一致性。以蝕刻技術來處理微米級的細節,結合使用雷射技術完成整體切割,這樣的製程不僅能減少加工步驟,還能降低生產成本。這對於需要大批量製造的半導體封裝測試設備來說,極具經濟效益。而且,這兩項技術與高品質材料的配合應用,幾乎不會對材料造成機械應力或熱應力,因此成品的尺寸穩定性和材料性能都能得到極佳的保障。
清潔IC晶片用隔網
厚度0.2mm, 方孔0.4x0.4mm
蝕刻技術與精密雷射切割的優勢
蝕刻與雷射雙重加工技術在半導體治具製作中的應用,展現了以下幾項主要優勢:
1. 高度精確
這兩種技術都能夠達到微米級的加工精度,滿足半導體行業對精密度的嚴格要求。特別是當治具需要應對複雜結構或微小尺寸的元件時,這種高精度的加工技術能夠確保每一個元件的定位和測試結果的準確性。
2. 靈活性強
精密雷射與蝕刻技術可以適應多種材料,並且能夠根據不同的設計需求進行靈活調整。無論是大規模的材料切割,還是微小的結構加工,這兩種技術都可以快速轉換並滿足不同應用場景的需求。
3. 加工效率高
雷射切割技術的加工速度非常快,可以在短時間內完成大面積的切割操作。而蝕刻技術則能同時對大面積材料進行處理,進一步提高了整體的生產效率。
精密雷射與蝕刻技術的製作流程
在測試治具與半導體封裝治具生產流程製作裡,精密雷射與蝕刻技術通常會結合使用,以實現最佳效果。具體的製作流程大致如下:
1. 設計與材料選擇
製作治具的第一步是進行設計。設計師會根據元件的需求和測試要求,繪製治具的結構圖。此過程通常使用CAD軟件來進行精確的設計,確保後續的製作過程能夠準確無誤。選擇材料時,通常會考慮到材料的硬度、導電性和抗腐蝕性等特徵。不鏽鋼、銅和鋁合金是製作半導體治具的常見材料。
2. 雷射切割與打孔
當設計圖完成後,雷射切割技術被用於切割出治具的主要外形。雷射切割能夠迅速、精確地將材料加工成所需的形狀。隨後,雷射打孔技術可以進行微孔的加工,這些微孔通常用來固定元件或提供測試接口。
3. 蝕刻處理
在雷射切割和打孔完成後,蝕刻技術將用來進一步加工細小結構。例如,治具上的表面導流溝槽,或者細小的測試探針通道,都可以通過蝕刻技術進行精密加工。這種技術能夠提供高度一致的加工效果,特別是在大規模生產過程中,蝕刻技術的重複精度非常高。
4. 表面處理與精加工
在完成主要的切割與蝕刻後,治具通常還需要進行表面處理與精加工。這包括清理材料表面上的殘留物、打磨邊緣,或進行額外的電解拋光以提高表面的光滑度。這些步驟有助於確保治具的長期穩定性和耐用性,提高測試治具製作精度,也可以避免因表面粗糙或不規則導致元件損壞或測試誤差。
結論
隨著半導體技行業技術創新,對封裝與測試治具的要求也將越來越高。未來,精密雷射與蝕刻技術將朝著更加自動化、智能化的方向發展。透過與人工智慧(AI)與大數據技術的結合,治具製作過程中的數據可以被即時分析與優化,從而進一步提高製造效率與產品品質。同時,隨著新材料的出現,這些精密加工技術也需要不斷進行升級與改進。例如,使用更高功率、更短波長的雷射光源來處理新型材料,或開發更高選擇性的蝕刻劑來應對複合材料的加工需求。這些技術的發展,將推動整個半導體產業向更高精度、更高可靠性的方向邁進。高精度雷射切割與微米級蝕刻處理技術在半導體封裝、測試治具製作中的應用,為現代電子產業的發展提供了強有力的技術支持。透過這些高精度加工技術,治具能夠以更高效、更可靠的方式提升先進封測技術。隨著半導體封裝技術提升,其相關技術也不斷進步,這些工藝將在未來扮演更加關鍵的角色,助力半導體產業的持續創新與升級。